Zepher Flight Labs of Bingen, Washington, is revolutionizing the industry with the next-generation VTOL UAS.
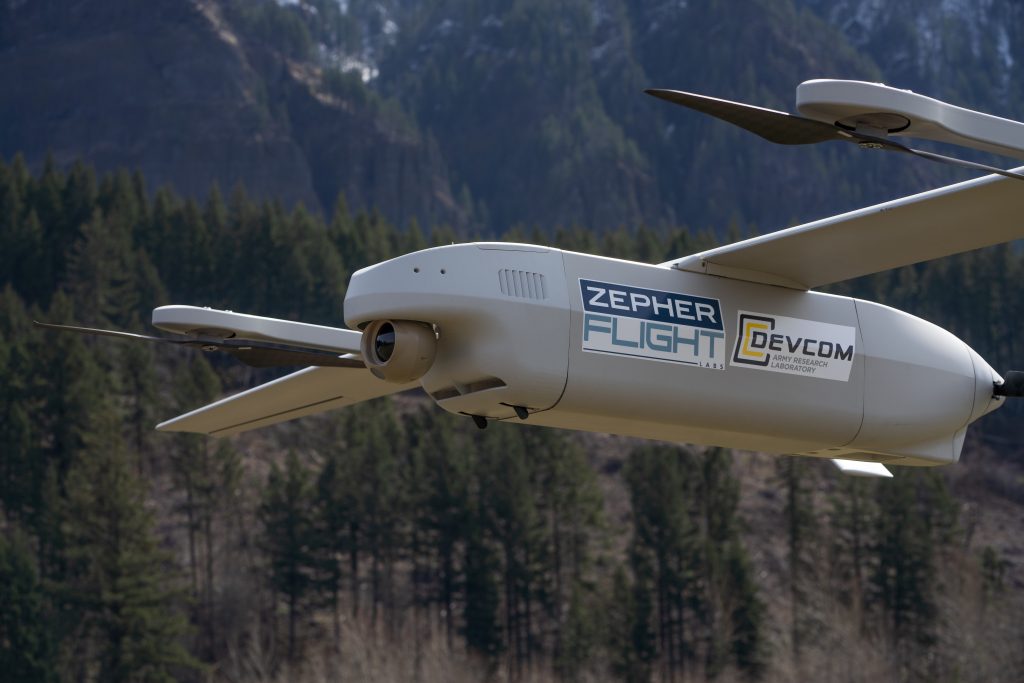
Rob Coatney is an aerospace engineer at Zepher Flight Labs (ZFL) in Bingen, Washington. Two years ago, ZFL secured a contract with the Army Research Laboratory to “develop technology that would improve the reliability, endurance, and acoustic signature of a Group II UAS in austere environments,” (according to a 2/23/23 press release). Coatney knew he wanted to be an aerospace engineer as early as eight. But now he is realizing his dream.
Coatney reflected on getting to where he is today, an aerospace engineer. “There’s one thing to getting an aerospace engineering degree — when you come out of college — you are an applied mathematician but at the same time, you have no experience.” He said it takes years to build on the theoretical background from college, along with learning what works, what doesn’t, and most importantly, what the customer wants.
Since 2010, he’s worked in the industry and has been a primary driver of the airframe for the vertical take-off and landing (VTOL) UAS, called the Z1. “I was able to make an efficient and manufacturable airframe,” he said. He’s also been involved with performance analysis, tooling, and structural design. “Most of what you see externally on the aircraft, I designed,” he said.
ZFL is building a hydrogen fuel cell powered UAS carrying 5kg/11-pound payloads. It is highly reliable, can be mass manufactured, and is modular. The luxury of ZFL is that they can develop the UAS to these high specifications and envision a new reality for the future of UAS because they have earned contracts with the Army Research Laboratory to fund the program.
Adam Stolz, president and CEO of ZFL, understands one of Coatney’s early learnings: knowing what the customer wants. Stolz has focused on the customer for most of the 19 years of his career. He worked for eight years as a civilian for the Department of Defense at the Naval Warfare Center, Crane Division, before making his way out West to work at Zepher, Inc., also in Bingen. He’s worked in business development and has spent time in customer outreach.
He said about the next generation UAS, “The new way of UASs and how the industry was going to use them – it was not going to look like it did.”
The concept of ZFL came from a plan to build a company that can focus on research and development of new technology, according to Jaime Mack, CEO and CTO of Zepher, Inc. She is the executive board member of ZFL and couched the two companies as sister companies. However, Stolz said that ZFL operates independently of Zepher, Inc.
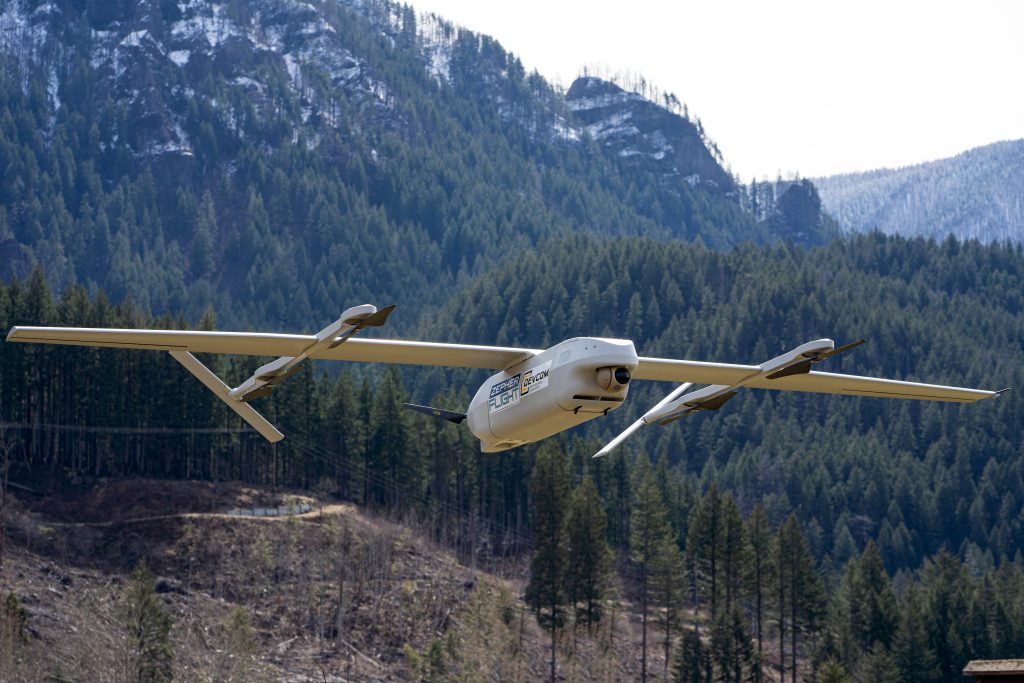
Mack said her main objective on the board of directors is to “shepherd the growth of the business financially in preparing for the technological challenges ahead. Not only to produce the current platform but also to continue innovating and growing the company.”
One of the company tenets is to design for manufacturability and mass production. They have a partner with the AS9100-certified Zepher, Inc. to conduct that work when they are ready. “Most UASs are not built for high volume, low cost. The reality is that the payloads end up costing three times as much as the structure,” Mack said. She aims to see the Z1 produced to get the product to “warfighters.” She added, “It doesn’t do any good to have a UAS for the warfighter if you can’t get it to the warfighter.”
Additionally, they are looking at the supply chain with this product, “We’ve seen with the global supply chain issues how critical it is to have manufacturability as your highest criteria. (We are) doing as much in-house as possible to eliminate global supply chain issues, as a barrier to on-time delivery.”
Stolz said the team at ZFL is ripe for this role of inventing a future UAS different from anything else on the market. “We saw a niche market and many UAS products, but the idea of the Z1 came from our aerospace engineer.” He noted that in addition to Coatney, they have a team of nine employees and are hiring more. “Our entire team has spent time in UAS companies. We’ve all seen it done elsewhere, and we feel there is a better way to create the right UAS platform now.”
Another plus of their working group is their vendors and service partners. “We consider the vendors and service partners a part of our overarching team.” He said for that reason, they are highly curated. They want to optimize their system so that everything comes together for the “right product.” They “heavily rely on them to bring it together in a new way,” he added. Service partners can provide engineering, testing, and development. They are also working to develop autonomous software with one of their partners.
He said, “We don’t need another product in this industry just to have it, but the Z1 is not just another UAS. It’s a different way to look at the whole feature set; the mission of tomorrow built this UAS.”
Coatney, Stolz, and Mack reflected that “There’s a better way to do UASs today.” Stolz added, “That’s not just the goal; that’s forward looking.” Hypothetically, he asked what the world looks for in commercial delivery, logistics, infrastructure, and inspection. Stolz thinks that with many innovations in the world, this development comes first from military applications, “You can see it daily in Ukraine,” he said.
Data gathering and inspection need the right tool, he observed observed. Also, he noted that without this kind of innovation, it wouldn’t make sense to have 1000 drones in the sky simultaneously because you’d need 5,000 to 10,000 people to operate and maintain them. They are working on an autonomous, quiet, and sustainable product. “The product’s robustness is through the build, maintenance, operation, and the ability to swap out components on missions; it will also need to be autonomous.”
Their contract with the Army calls for prototypes and a functional, reproducible UAS. The product will be used to “participate in military exercises within the Indo-Pacific Command area of operation, which encompasses the Pacific Ocean, parts of Russia, China, Mongolia, Korea, and Japan; the Indian Ocean to Antarctica; Australia, New Zealand, Antarctica, and Hawaii.” (Wikipedia, United States, Indo-Pacific Command).
Summary
Zepher Flight Labs aims to build the next generation of UAS that is built better and can be reproduced. The team at ZFL is highly experienced and serious about delivering on their contracted work with the next generation UAS. Mack said, “ZFL is pragmatic about building the best tool we can for the military customer, without ego.” She noted that ZFL is very customer driven. “We are most obsessed with serving the warfighter. The design and thought process of the Z1 is — as much as possible — from the user’s point of view, not the engineers. That speaks volumes about the resulting product.”
Attributes of the Z1
- Reliability – They are creating a UAS that is a highly reliable tool, and reliability is a big part of the design.
- Mass manufacturing – This UAS has been designed for manufacturing. Instead of making one or two models, they could manufacture thousands.
- Modularity in architecture and operations – The entire aircraft can be assembled in minutes. They are creating airframe and payload modules with plug-and-play features.
Contact Info
Zepher Flight Labs
310 South Larch Street
Bingen, Washington 98605
info@zepherflight.com
www.zepherflight.com